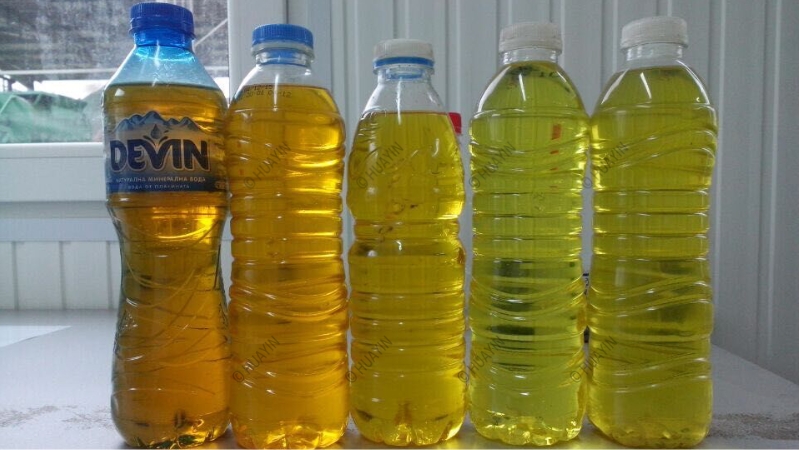
PVC (polyvinyl chloride) is a widely used plastic material in construction, electronics, and healthcare industries. However, PVC plastic is unsuitable as a raw material for pyrolysis projects.
The chemical properties of PVC plastics determine their unsuitability in pyrolysis processes. PVC plastic is a polymer containing chlorine elements. When pyrolysis is carried out under high-temperature heating conditions, a large amount of harmful substances such as hydrogen chloride and ethylene dichloride are produced. These harmful substances not only cause corrosion to plastic pyrolysis plants, greatly shorten the service life of the equipment but also pose potential risks to the health of operators.
The characteristics of the pyrolysis process also limit the use of PVC plastics. Pyrolysis is the process of cracking raw materials under high-temperature and anaerobic conditions to produce fuel oil and waste gas. However, PVC plastic is prone to decompose and release harmful gases at high temperatures, which increases the difficulty of disposing of waste gas during the pyrolysis process and can also cause environmental pollution.
PP/PE/PS/ABS, plastic bags, paper mill waste, landfill plastic, plastic cable skin, and other plastics can all be used for pyrolysis and making fuel oil, with an oil yield of around 30-95%. Different types of plastics have significant fluctuations in their oil yield. In addition to plastics, tires, rubber, oil sludge, medical waste, etc. are also suitable as raw materials for pyrolysis, achieving waste recycling and reuse, which is more in line with the requirements of sustainable development.
Whether your raw materials are plastic, tires, aluminum-plastic, or oil sludge, we can customize the material and design of the pyrolysis machine according to the characteristics of the raw materials you want to process, helping you achieve efficient and stable production. If you have any interests, please leave your contact information for consultation!