recycling of used tires
Pyrolysis technology offers a practical solution to recycling of used tires. The original raw materials to make tires which are:
Rubber (natural and synthetic) 41%
Fillers (carbon black, silica, carbon, chalk…) 30%
Reinforcing materials (steel, polyester, rayon, nylon) 15%
Plasticizers (oils and resins) 6%
Chemicals for vulcanization (sulphur, zinc oxide…) 6%
Anti-ageing agents and other chemicals 2%
are 100% recycled and become usable products with marketing values. Tire pyrolysis plant not only solves the environmental problem of used tires, but also create a profitable business with high ROI.
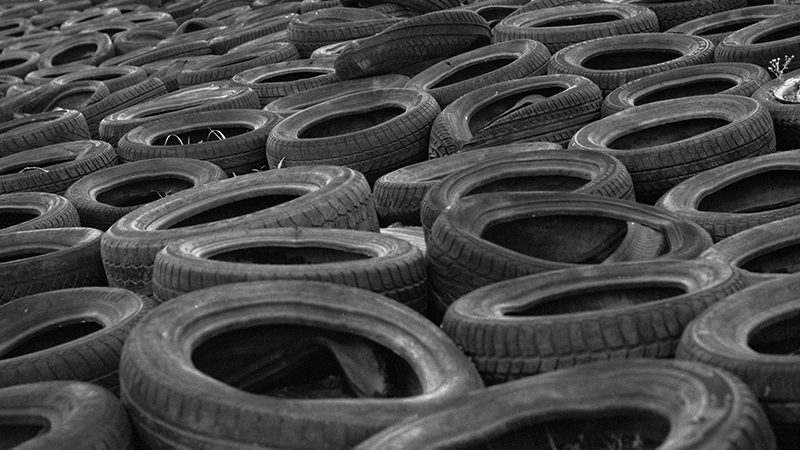
production ratio
The production ratio of output products depend on the original component of raw materials to make tires.
Known as fuel oil, pyrolysis oil, heating oil, furnace oil. Used as industrial fuel for cement plant, steel plant, metallurgical plant, glass plant, power plant etc.
Used as raw materials for rubber and plastic industries after further processing. Or used as heating fuel.
Sold to scrap metal dealers.
Known as combustible gas or non-condensable gas. Routed to gas burners of heating system as fuel supply.
running process
Typical running process and production time to process 10 tons of used tires.
Using hydraulic feeder to load used tires into pyrolysis reactor. It can load whole tires without shredding. The pyrolysis reactor rotates in feeding direction. Keeps feeding until the reactor is fully loaded. Usually it takes 2.5 hours to load 10 tons of used tires.
When feeding is finished, closes the feeding port then ignites the heating system. The internal temperature goes up slowly in the first 2 hours.
Used tires break down into gas state and solid state under pyrolysis reaction. The gas state enters condensing system, gets liquified and becomes liquid fuel. The oil production process lasts 10 hours. The solid state that is carbon black and steel wire stays inside pyrolysis reactor waiting for discharging.
When oil production is finished, leaves the machine to cool down for 3 hours before discharging.
Discharges carbon black from reactor by U-shape conveyor. It takes around 2.5 hours.
Discharges steel wire mass from reactor by winch. It takes around 30 minutes.
Model A series
- Unit Capacity: 5/10/15 tons
- Basic choice to start
- Medium emission control
- Onsite installation
Model C series
- Unit Capacity: 5/10/15 tons
- Advanced choice
- High emission control
- Quick installation
Model F series
- Unit Capacity: 750/4000kg
- Installation-FREE
- Low shipping cost
- Modular design
Model M series
- Unit capacity: 10kg
- Mini scale model
- Fully operational
- Installation-FREE
Model S series
- Unit capacity: 30/50 tons
- Continuous type
- High-end choice
- Onsite installation